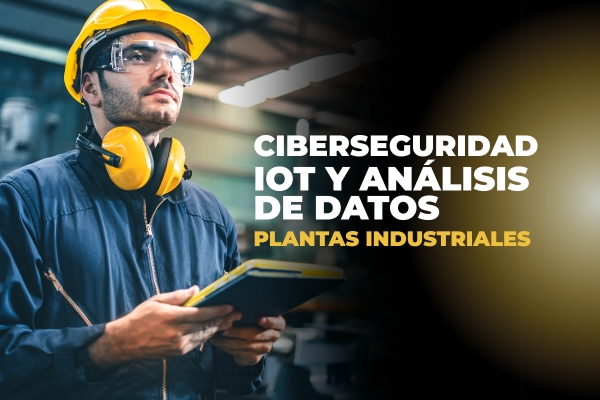
HercoTV
Podcast
Descubre cómo la ciberseguridad, el IoT y el análisis de datos transforman las plantas industriales, mejorando la eficiencia, seguridad y mantenimiento.
La transformación digital del mantenimiento industrial
En la era de la Industria 4.0, la ciberseguridad, el Internet de las Cosas (IoT) y el análisis de datos se han convertido en pilares fundamentales para optimizar los procesos de mantenimiento en plantas industriales. Estas tecnologías emergentes ofrecen soluciones innovadoras que permiten a las empresas mejorar la eficiencia, reducir costes y garantizar la seguridad de sus operaciones.
Desde Herco sabemos de la importancia de estar a la vanguardia de estos avances. Hoy, vamos a compartir contigo las claves para aprovechar al máximo el potencial de la ciberseguridad, el IoT y el análisis de datos en tus procesos de mantenimiento. Ampliando la información de la que hablamos en nuestro podcast «Inteligencia artificial y análisis de datos en el mantenimiento industrial» con Fernando Val, CEO de ISOMATIC.
Ciberseguridad: Protegiendo la infraestructura crítica
La ciberseguridad es fundamental en la era digital, especialmente en entornos industriales donde la interconexión de sistemas y la dependencia tecnológica son cada vez mayores. Un ataque cibernético puede tener consecuencias devastadoras, desde la interrupción de la producción hasta daños físicos en la planta.
Por eso, es crucial implementar un enfoque integral de ciberseguridad que abarque tanto los sistemas de Tecnología de la Información (TI) como los de Tecnología Operacional (TO). Algunas estrategias clave incluyen:
1. Adoptar el modelo de «Confianza Cero»
El modelo de «Confianza Cero» es una estrategia de seguridad que se basa en la premisa de que no se debe confiar en ningún usuario, dispositivo o aplicación por defecto. En su lugar, se debe verificar y autorizar continuamente el acceso a los recursos, independientemente de dónde se encuentren los usuarios o los dispositivos. Esto ayuda a prevenir el acceso no autorizado y a mitigar los riesgos de amenazas internas y externas.
2. Integrar la ciberseguridad en la gestión de riesgos y seguridad de procesos
La ciberseguridad debe estar integrada en los procesos de gestión de riesgos y seguridad de procesos de la empresa. Esto implica identificar y evaluar los riesgos cibernéticos, implementar controles adecuados y monitorizar continuamente la postura de seguridad. Además, es importante alinear las estrategias de ciberseguridad con los objetivos de negocio y las normas y regulaciones aplicables.
3. Implementar soluciones de monitorización y detección de amenazas
La implementación de soluciones de monitorización y detección de amenazas en tiempo real es fundamental para identificar y responder rápidamente a los incidentes de seguridad. Estas soluciones pueden utilizar técnicas como el análisis de tráfico de red, la detección de anomalías y la inteligencia artificial para identificar actividades sospechosas y generar alertas oportunas.
4. Capacitar y sensibilizar al personal
El factor humano es crucial en la ciberseguridad. Es importante capacitar y sensibilizar a todo el personal sobre buenas prácticas de ciberseguridad, como la gestión de contraseñas, la detección de phishing y la respuesta ante incidentes. Esto ayuda a crear una cultura de seguridad y a reducir el riesgo de errores humanos que puedan comprometer la seguridad.
Al proteger tu infraestructura crítica mediante estas estrategias, no solo evitas costosos incidentes, sino que también sientas las bases para una mayor eficiencia y fiabilidad en tus operaciones de mantenimiento. La ciberseguridad es una inversión fundamental para garantizar la continuidad y la competitividad de tu negocio en la era digital.
Conectando la planta con IoT para una mejor toma de decisiones
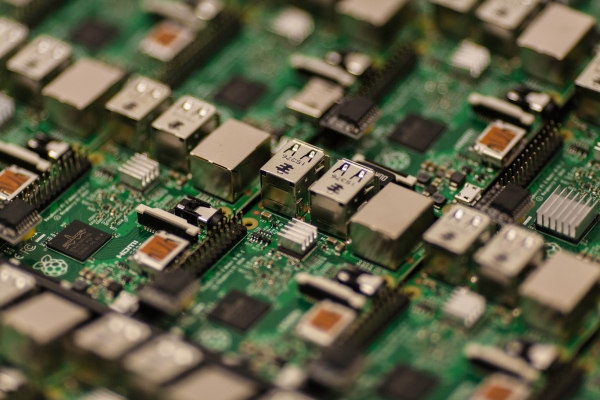
El Internet de las Cosas (IoT) ha revolucionado la forma en que monitorizamos y gestionamos los activos industriales en las plantas. Al integrar sensores y dispositivos conectados a lo largo de toda la planta, puedes recopilar una gran cantidad de datos en tiempo real sobre el estado de los equipos.
1. Implementar un mantenimiento predictivo más efectivo
Esta información obtenida a través del IoT permiten anticiparte a posibles fallos en los equipos. Mediante el análisis de los datos de sensores como vibración, temperatura, presión, etc., puedes detectar patrones que indiquen un deterioro inminente. Esto te permite implementar un mantenimiento predictivo más efectivo, programando intervenciones antes de que ocurran averías imprevistas.
2. Optimizar la programación del mantenimiento
Además, el IoT ayuda a optimizar la programación del mantenimiento y reducir los tiempos de inactividad. Al monitorizar en tiempo real el rendimiento y el estado de los equipos, puedes ajustar los planes de mantenimiento preventivo, evitando paradas innecesarias y maximizando la disponibilidad de la planta.
3. Mejorar la eficiencia energética y sostenibilidad
Pero el IoT va más allá de la simple recopilación de datos. Al combinar estas capacidades con técnicas avanzadas de análisis, puedes transformar esos datos en información accionable que te ayude a tomar decisiones más informadas y estratégicas. Por ejemplo, puedes utilizar los datos de consumo energético para identificar oportunidades de mejora en la eficiencia y sostenibilidad de los procesos.
4. Garantizar la seguridad de los trabajadores
El IoT permite monitorizar variables ambientales como temperatura, humedad y niveles de gases, lo que ayuda a garantizar la seguridad y el bienestar de los trabajadores en la planta. Puedes recibir alertas tempranas ante condiciones peligrosas y tomar medidas preventivas.
Al integrar el IoT en tu planta industrial, obtienes una visibilidad sin precedentes sobre el estado de tus activos. Esto te ayuda a tomar decisiones más informadas y estratégicas, anticipándote a problemas, optimizando procesos y mejorando la seguridad y sostenibilidad de nuestras operaciones. El IoT se ha convertido en una herramienta indispensable para lograr una mayor eficiencia y competitividad en el entorno industrial.
Análisis de datos: Transformando los datos en ventajas competitivas
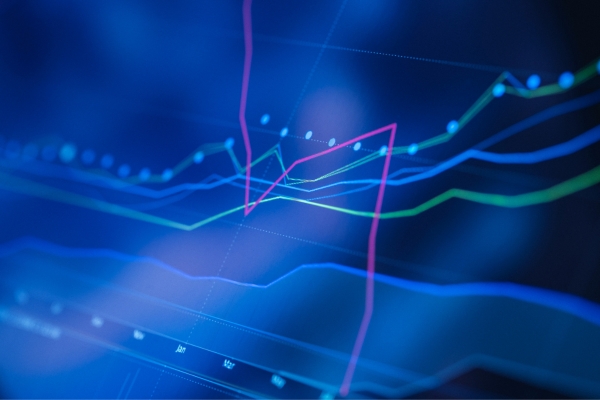
El volumen y la complejidad de los datos generados en una planta industrial pueden ser abrumadores. Sin embargo, al aplicar técnicas de análisis de datos avanzadas, puedes extraer información que te permita optimizar tus operaciones de mantenimiento.
Algunas aplicaciones clave del análisis de datos en el mantenimiento industrial incluyen:
1. Detección temprana de anomalías y predicción de fallos en equipos
Mediante el análisis de datos históricos de rendimiento de los equipos, puedes desarrollar modelos predictivos que te permitan anticiparte a posibles fallos. Esto te ayudará a planificar el mantenimiento de forma proactiva, reduciendo los tiempos de inactividad y los costes asociados.
2. Identificación de patrones y tendencias que guíen la toma de decisiones
Al analizar los datos de mantenimiento, producción, energía y otros sistemas, se pueden identificar patrones y tendencias que te ayuden a tomar decisiones más informadas sobre la gestión de tus activos. Esto incluye optimizar los planes de mantenimiento, ajustar los procesos y mejorar la eficiencia general de la planta.
3. Optimización de los planes de mantenimiento preventivo y predictivo
Combinando el análisis de datos históricos con técnicas avanzadas como el aprendizaje automático, se pueden desarrollar modelos que te permitan predecir con mayor precisión cuándo se producirán fallos en los equipos. Esto permite optimizar los planes de mantenimiento, reduciendo los costes y mejorando la disponibilidad de los activos.
4. Mejora de la eficiencia energética y la sostenibilidad de los procesos
El análisis de datos de consumo energético, emisiones y otros indicadores ambientales permite identificar oportunidades para mejorar la eficiencia y reducir el impacto ambiental en las operaciones. Esto incluye optimizar el uso de energía, reducir los residuos y mejorar la sostenibilidad general de la planta.
5. Análisis de riesgos y evaluación del impacto de posibles incidentes
Mediante el análisis de datos de seguridad, incidentes y otros factores de riesgo, puedes evaluar y mitigar los riesgos asociados a tus operaciones. Esto ayuda a tomar decisiones más informadas sobre la gestión de la seguridad y la preparación ante posibles emergencias.
Al aprovechar el poder del análisis de datos, puedes transformar tus datos en ventajas competitivas tangibles, como una mayor disponibilidad de los equipos, una reducción de los costes de mantenimiento y una mayor satisfacción de los clientes. Esto consigue mejorar la eficiencia, la fiabilidad y la sostenibilidad de las operaciones de mantenimiento.
Integrando las piezas del rompecabezas
La clave para aprovechar al máximo el potencial de la ciberseguridad, el IoT y el análisis de datos radica en su integración efectiva. Estos elementos deben trabajar de manera sinérgica para crear un ecosistema industrial resiliente, eficiente y orientado al futuro.
Algunas estrategias clave para lograr esta integración incluyen:
- Adoptar un enfoque holístico de gestión de activos que combine mantenimiento predictivo, ciberseguridad y sostenibilidad.
- Implementar plataformas de IoT que permitan la recopilación, el análisis y la visualización de datos en tiempo real.
- Capacitar y empoderar a los equipos de mantenimiento para que aprovechen estas tecnologías de manera efectiva.
- Fomentar una cultura de innovación y mejora continua en toda la organización.
Al integrar estas piezas del rompecabezas, podrás transformar tu planta industrial en un modelo de eficiencia, seguridad y sostenibilidad, posicionándote como un líder en tu sector.
Liderando el futuro del mantenimiento industrial
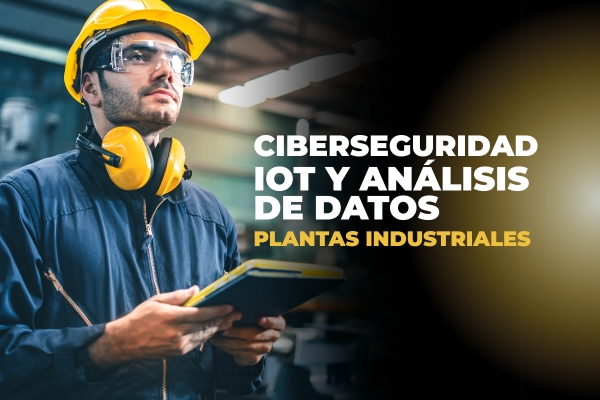
En un mundo cada vez más digitalizado, la ciberseguridad, el IoT y el análisis de datos se han convertido en pilares fundamentales para el mantenimiento industrial. Estas tecnologías emergentes ofrecen soluciones innovadoras que te permitirán mejorar la eficiencia, reducir costes y garantizar la seguridad de tus operaciones.
Como responsable de mantenimiento industrial, tienes la oportunidad de liderar esta transformación digital y posicionar a tu empresa como un referente en el sector. Al adoptar un enfoque integral que combine estas tecnologías, podrás crear un ecosistema industrial resiliente, eficiente y orientado al futuro.
Recuerda, el éxito no se logra de la noche a la mañana. Requiere de un compromiso constante con la innovación, la mejora continua y el desarrollo de las capacidades de tu equipo. Pero el esfuerzo valdrá la pena, ya que te permitirá marcar la diferencia en un mundo cada vez más competitivo y exigente.
¿Estás listo para liderar el futuro del mantenimiento industrial? Te animamos a suscribírte a nuestro podcast y donde en cada episodio, encontrarás consejos y estrategias que te ayudarán a transformar tu planta industrial en un modelo de eficiencia, seguridad y sostenibilidad.
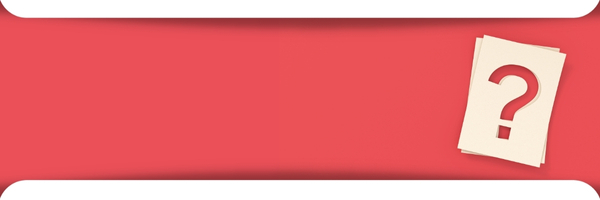
Preguntas para reflexionar
- ¿Cómo podrías integrar la ciberseguridad, el IoT y el análisis de datos en tu estrategia de mantenimiento industrial para mejorar la eficiencia y la seguridad de tus operaciones?
- ¿Qué barreras o desafíos podrías enfrentar al implementar estas tecnologías en tu planta y cómo podrías superarlos?
- ¿Cómo podrías involucrar y capacitar a tu equipo de mantenimiento para que aprovechen al máximo el potencial de la ciberseguridad, el IoT y el análisis de datos?
Respondemos a tus preguntas sobre IoT en la industria y la importancia de la ciberseguridad
¿Qué es la ciberseguridad industrial y por qué es importante en entornos industriales?
La ciberseguridad industrial es el conjunto de prácticas, tecnologías y procesos diseñados para proteger los sistemas industriales, redes y datos contra amenazas digitales. Su importancia radica en que los sistemas de control industrial (como SCADA) y equipos industriales gestionan infraestructuras críticas donde un ciberataque podría provocar no solo pérdida de datos, sino también paradas de producción, daños físicos o incluso riesgos para la seguridad de las personas. Con la creciente interconexión de los sistemas en entornos industriales, la superficie de ataque ha aumentado, haciendo que la protección de estos entornos sea una prioridad absoluta para garantizar la continuidad operativa.
¿Cómo afecta la Industria 4.0 a la seguridad en entornos industriales?
La Industria 4.0 ha transformado radicalmente los procesos industriales al integrar tecnologías como la automatización industrial, dispositivos IoT y sistemas interconectados. Si bien esto ha mejorado la eficiencia y la productividad, también ha multiplicado las vulnerabilidades y la superficie de ataque. Los ciberdelincuentes pueden ahora obtener acceso no autorizado a través de más puntos de entrada, desde sensores IoT hasta sistemas de control industrial. Esta evolución ha obligado a las empresas a replantear sus estrategias de ciberseguridad industrial, implementando medidas de seguridad más robustas que protejan tanto la OT (Tecnología Operacional) como los nuevos componentes digitales integrados en la producción.
¿Cuáles son los principales tipos de vulnerabilidad en sistemas con Industrial IoT?
En sistemas con Industrial IoT, las principales vulnerabilidades incluyen: configuraciones predeterminadas o débiles en dispositivos IoT, falta de cifrado de datos en las comunicaciones entre sensores y sistemas centrales, actualizaciones de firmware irregulares, autenticación insuficiente para acceder a los sistemas de control, integración deficiente entre tecnologías OT tradicionales y modernas, y escasa segmentación de redes. Particularmente preocupante es la conexión de equipos industriales antiguos (no diseñados con la seguridad en mente) a redes modernas, creando «puertas traseras» que los ciberatacantes pueden aprovechar para comprometer toda la infraestructura y obtener acceso a datos críticos de producción.
¿Qué mejores prácticas en ciberseguridad industrial deberían implementarse para proteger los sistemas industriales?
Las mejores prácticas en ciberseguridad industrial incluyen: implementar segmentación de redes para aislar sistemas críticos, establecer políticas estrictas de control de acceso basadas en el principio de mínimo privilegio, mantener actualizados todos los sistemas y firmware, realizar evaluaciones periódicas de vulnerabilidad, implementar sistemas de detección y respuesta a incidentes específicos para entornos OT, cifrar todas las comunicaciones, especialmente las que involucran sensores IoT, capacitar regularmente al personal sobre amenazas digitales, desarrollar planes de respuesta a incidentes de seguridad, realizar copias de seguridad regulares, y colaborar con expertos en seguridad industrial para evaluaciones externas. Estas medidas deben adaptarse constantemente para responder a las nuevas amenazas que surgen en el panorama de la ciberseguridad.
¿Cómo pueden los sensores IoT mejorar la seguridad industrial mientras se mantienen protegidos?
Los sensores IoT pueden mejorar significativamente la seguridad industrial al proporcionar monitorización en tiempo real de condiciones críticas como temperatura, presión, vibraciones o fugas, permitiendo la detección temprana de anomalías que podrían representar riesgos de seguridad. Sin embargo, para mantener estos dispositivos protegidos, es esencial implementar medidas como: cifrado de datos en todas las comunicaciones, autenticación robusta para cada sensor, actualizaciones regulares de firmware, segmentación de red para aislar los sensores de sistemas críticos, monitorización constante del tráfico de datos para detectar comportamientos anómalos, y la implementación de una arquitectura de seguridad por capas. Un enfoque equilibrado permite aprovechar los beneficios de los sensores IoT para la automatización y la seguridad física mientras se minimizan los riesgos cibernéticos asociados.
¿Cómo se debe gestionar la seguridad en la convergencia entre OT (Tecnología Operacional) y TI en la automatización industrial?
La gestión de la seguridad en la convergencia OT-TI requiere un enfoque holístico que reconozca las diferencias fundamentales entre ambos entornos. Es recomendable establecer equipos multidisciplinarios que entiendan tanto los sistemas de control industrial como la tecnología de la información, implementar arquitecturas de referencia específicas para esta convergencia, utilizar tecnologías de virtualización para aislar sistemas críticos, establecer políticas de acceso unificadas, implementar soluciones de monitorización capaces de entender protocolos industriales y TI, desarrollar procedimientos de respuesta a incidentes que consideren el impacto en procesos industriales, y mantener procesos de gestión del cambio que evalúen el impacto de seguridad de cualquier modificación. Esta convergencia, aunque desafiante, es fundamental para aprovechar plenamente los beneficios de la automatización en la era de la Industria 4.0.
¿Qué papel juega el análisis de datos en la prevención de ciberataques en plantas industriales?
El análisis de datos se ha convertido en una herramienta fundamental para la prevención de ciberataques en entornos industriales. Mediante técnicas avanzadas de análisis, es posible establecer patrones normales de comportamiento en los sistemas de control industrial y detectar anomalías que podrían indicar un ciberataque en curso. Las soluciones de análisis pueden procesar datos de múltiples fuentes (sensores IoT, sistemas SCADA, registros de red) para identificar correlaciones que serían imposibles de detectar manualmente. Además, las tecnologías de aprendizaje automático pueden adaptarse continuamente para reconocer nuevas amenazas y vulnerabilidades, ofreciendo protección contra técnicas de ataque emergentes. Esta capacidad de análisis proactivo permite a los equipos de seguridad industrial anticiparse a las brechas de seguridad antes de que causen daños significativos.
¿Cuáles son los principales incidentes de seguridad que afectan a los sistemas industriales y cómo prevenirlos?
Los principales incidentes incluyen ataques de ransomware específicos para entornos industriales, ataques de denegación de servicio que paralizan la producción, compromisos de la cadena de suministro, explotación de vulnerabilidades en dispositivos IoT, ataques de ingeniería social dirigidos a operadores, y manipulaciones de datos que afectan la integridad de los procesos. Para prevenirlos, es esencial implementar medidas como: segmentación de red para sistemas críticos, programas regulares de concienciación y formación del personal, gestión rigurosa de parches y actualizaciones adaptada a entornos OT, control de acceso basado en roles, monitorización continua con sistemas de detección específicos para entornos industriales, y evaluaciones periódicas de vulnerabilidad. Además, el desarrollo de un plan de respuesta a incidentes que considere las particularidades de los entornos industriales es fundamental para minimizar el impacto cuando ocurra un ciberataque.
¿Cómo afrontar las nuevas amenazas en ciberseguridad industrial que surgen con la evolución tecnológica?
Para afrontar las nuevas amenazas en ciberseguridad industrial, las organizaciones deben adoptar una mentalidad de mejora continua y adaptación. Esto incluye: mantenerse informado sobre las últimas tendencias en ciberataques a través de la participación en comunidades de intercambio de información, implementar arquitecturas de seguridad adaptativas que puedan evolucionar, invertir en tecnologías emergentes como la inteligencia artificial para la detección de amenazas, realizar ejercicios de simulación de ciberataques específicos para entornos industriales, desarrollar capacidades de respuesta rápida, establecer colaboraciones con proveedores para abordar vulnerabilidades en dispositivos y sistemas, y fomentar una cultura organizacional donde la seguridad sea responsabilidad de todos. La clave está en la capacidad de anticiparse y adaptarse a un panorama de amenazas en constante cambio, especialmente en lo relacionado con dispositivos IoT y sistemas de automatización cada vez más complejos.
En definitiva, integrar la ciberseguridad, el IoT y el análisis de datos en las plantas industriales no es una opción, sino una necesidad para quienes desean mantenerse competitivos en la era digital.