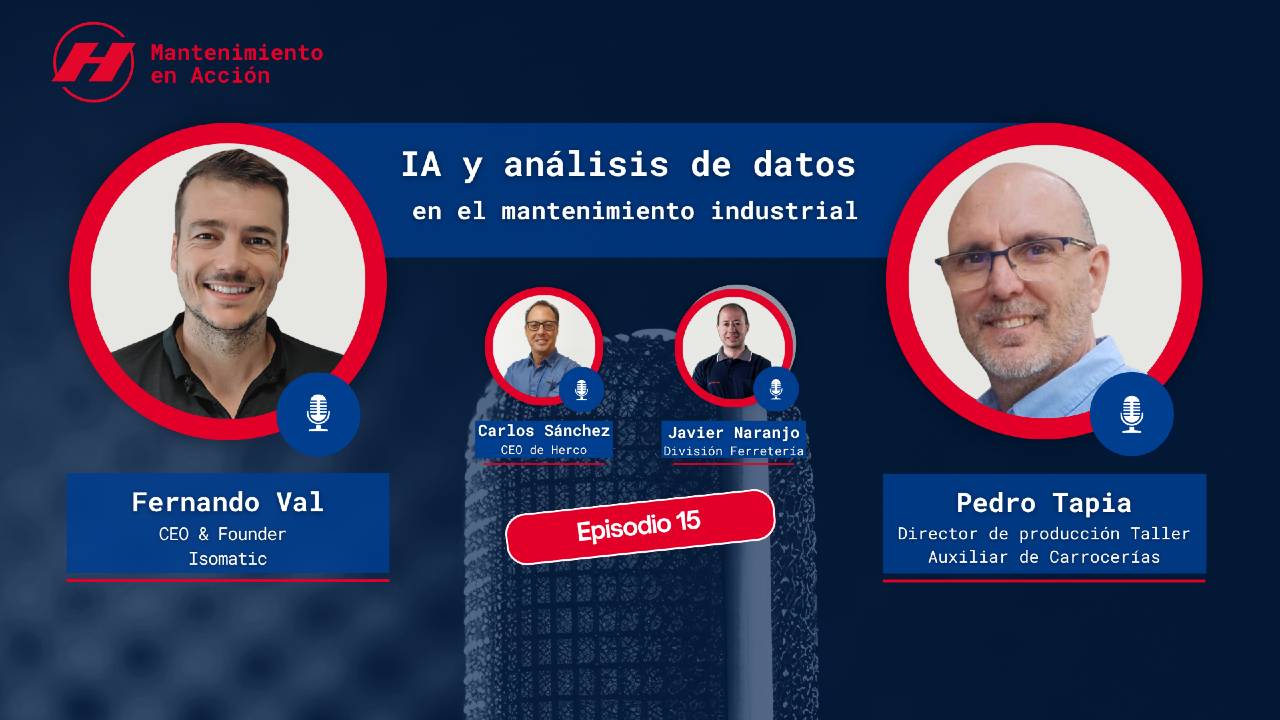
HercoTV
Podcast
La inteligencia artificial en el mantenimiento industrial está marcando un antes y un después en la forma de gestionar activos, anticipar fallos y mejorar la eficiencia operativa. Gracias al análisis de datos en tiempo real y al uso de algoritmos predictivos, las empresas pueden transformar su enfoque, pasando de un mantenimiento reactivo a uno inteligente, basado en la prevención y la optimización continua. En este episodio del podcast “Mantenimiento en Acción”, abordamos cómo esta revolución tecnológica ya está impactando en plantas de todos los tamaños y sectores.
La inteligencia artificial y el análisis de datos están transformando el mantenimiento en las plantas industriales
¿Te suena familiar esa sensación de estar apagando incendios constantemente en tu planta, persiguiendo averías inesperadas y lidiando con paradas que parecen llegar siempre en el peor momento? ¿Notas que las averías y las ineficiencias cuestan demasiado, pero no sabes por dónde empezar a ponerle remedio? Si te reconoces en estas situaciones, tienes que escuchar este episodio de “Mantenimiento en Acción”. En este post te contamos lo más destacado del programa y por qué puede suponer un antes y un después para tu día a día. ¡Sigue leyendo!
Un encuentro de expertos apasionados por el mantenimiento
En este episodio de “Mantenimiento en Acción”, nos acompañan voces con una experiencia y un entusiasmo difícil de igualar en el sector. Por un lado, Javier Naranjo y Carlos Sánchez, anfitriones e impulsores del podcast, a quienes ya conocerás si eres oyente habitual. Ellos abren el apetito informativo con actualidad y tendencias, y conducen la conversación de manera cercana y didáctica, pensada para quienes realmente viven el mantenimiento desde dentro.
El plato fuerte, sin embargo, llega de la mano de Fernando Val, CEO de ISOMATIC, una empresa referente en integración de soluciones de automatización y robótica industrial. Fernando aporta una visión muy realista sobre los retos, pero también sobre las increíbles oportunidades que ofrece la digitalización para el área de mantenimiento. Por último, Pedro Tapia, nuestro querido “profesor” del «Consejo del Experto», redondea el episodio con un análisis práctico sobre el salto del mantenimiento preventivo al predictivo.
Noticias: Innovación en herramientas de precisión y el valor de la neumática
Como no podía ser de otra manera, el episodio arranca con una sección de noticias que aporta contexto y conecta la actualidad global con el día a día en planta. Javier y Carlos desgranan la adquisición de Norbar Torque Tools por Snap-On, una jugada estratégica que concentra aún más especialización en herramientas de control de par y calibración. ¿Por qué debería interesarte esto? Porque la precisión y fiabilidad en el par de apriete no es negociable en muchísimas industrias: desde la energía hasta la alimentaria. Fallar aquí puede ser catastrófico. La integración de Norbar en Snap-On vaticina innovación y oferta más potente en herramientas motorizadas y digitalizadas, justo en el corazón de la nueva industria conectada.
Después, el foco se pone sobre la neumática, ese “clásico” indispensable en cualquier fábrica. Los presentadores repasan su origen, principios de funcionamiento y, sobre todo, por qué sigue tan vigente: es limpia, sencilla, segura contra explosiones y fácil de mantener. Además, su coste es relativamente bajo y su velocidad de actuación sigue haciendo sombra a muchas otras tecnologías. ¿Qué conclusión sacamos aquí? El mantenimiento inteligente empieza por la base: entender y dominar los componentes fundamentales del proceso industrial, desde la herramienta al sistema completo.
Fernando Val: El futuro ya está aquí… y es digital, colaborativo y predictivo
La gran entrevista del episodio pone el foco donde más duele (y donde más se puede ganar): la digitalización del mantenimiento y la explotación de los datos de máquina en tiempo real. Fernando Val, liderando ISOMATIC, comparte aprendizajes y estrategias para transformar incluso los parques de maquinaria más heterogéneos y anticuados, gracias a la integración de sensores y tecnologías como IoT, visión artificial, gemelo digital y realidad aumentada.
Uno de los grandes desafíos que destaca Fernando es la convivencia de maquinaria vieja y nueva. Muchas plantas quieren empezar a tomar datos para optimizar, pero las máquinas clásicas no estaban preparadas para ello. Aquí entra el famoso “retrofitting”: actualizar equipos antiguos para poder conectarlos y explotar sus datos, aunque suponga un esfuerzo extra inicial.
Pero, ¿y cuando ya tienes los datos? Aquí es donde la inteligencia artificial revoluciona el juego. El mantenimiento pasa de ser reactivo e intuitivo a ser predictivo y objetivo. La IA permite analizar enormes volúmenes de datos en tiempo real, anticipar fallos, priorizar intervenciones e, incluso, adaptar la producción a las condiciones reales de cada momento. Además, el análisis de datos y la colaboración entre diferentes empresas –incluso compartiendo información anónima– da lugar a algoritmos más precisos y menos incertidumbre, algo fundamental para las PYMEs que no tienen parques gigantes de equipos conectados.
Entre los retos más recientes, Fernando advierte sobre la importancia de la ciberseguridad y la calidad de los datos. No se trata solo de recoger datos, sino de hacerlo bien y de protegerlos. La revolución digital del mantenimiento no depende tanto de la tecnología en sí, sino de la gestión inteligente, segura y colaborativa de la información.
Pedro Tapia: De la prevención a la predicción, un salto (muy) rentable
Pedro Tapia aterriza toda la teoría en terreno práctico con su habitual “Consejo del Experto”. El foco: la transición del clásico mantenimiento preventivo —tan extendido en grandes empresas, pero menos en pymes— al mantenimiento predictivo, apoyado en sensores, cloud y modelos de machine learning. Pedro subraya dos puntos de dolor reales: muchas PYMEs siguen instaladas en el correctivo y, aunque las grandes avanzan, la gestión del cambio sigue siendo el principal obstáculo (falta de sistemas, burocracia, resistencia al cambio y poca capacitación digital).
¿Por qué deberías plantearte dar el salto al mantenimiento predictivo? No es solo una moda. Identificar anomalías antes de que causen paradas, reducir repuestos, optimizar recursos y minimizar intervenciones innecesarias suponen una verdadera ventaja competitiva. Eso sí, Pedro es claro: la evolución debe ser gradual, priorizando activos críticos y asegurando una formación continua del personal para aprovechar todo el potencial de la nueva tecnología.
El futuro inmediato pasa, según Pedro, por redes colaborativas de datos, gemelos digitales, automatización avanzada y mantenimiento prescriptivo, donde el propio sistema no solo predice el fallo, sino que recomienda qué hacer, cuándo, con qué repuesto y hasta con qué técnico.
El dato como motor del cambio: No te quedes atrás
Lo que queda claro tras escuchar el episodio es que la digitalización y el análisis avanzado de datos no son solo una tendencia, son el gran catalizador de la transformación en la gestión del mantenimiento industrial, y una palanca de competitividad clave tanto para grandes como para pequeñas empresas. Esperar a que la “ola” pase es quedarse fuera del futuro del sector.
¿Quieres saber más y escuchar experiencias reales y consejos accionables? No dejes pasar el episodio completo de “Mantenimiento en Acción”. Suscríbete al podcast y únete a una comunidad que avanza unida hacia el mantenimiento inteligente y predictivo.
Escúchalo, comparte y coméntalo en redes. El futuro del mantenimiento industrial empieza ahora. ¡No te lo pierdas!
Preguntas frecuentes sobre inteligencia artificial en mantenimiento y análisis de datos
¿Cómo funciona la inteligencia artificial en el mantenimiento industrial?
La inteligencia artificial en el mantenimiento industrial funciona mediante la recolección y análisis de grandes volúmenes de datos provenientes de equipos y sensores. Estos sistemas utilizan algoritmos de aprendizaje automático para identificar patrones, predecir fallos y recomendar acciones preventivas. La IA procesa datos históricos y en tiempo real para detectar anomalías antes de que causen averías, lo que permite a las empresas programar el mantenimiento de manera más efectiva, reducir el tiempo de inactividad y optimizar la vida útil de los equipos. Las soluciones de IA transforman la gestión de activos, pasando de un enfoque reactivo a uno predictivo y proactivo.
¿Cuáles son los beneficios del mantenimiento predictivo en la industria?
El mantenimiento predictivo en la industria ofrece múltiples ventajas: reduce drásticamente el tiempo de inactividad no planificado al anticipar fallos antes de que ocurran; optimiza los costos operativos al programar intervenciones de mantenimiento solo cuando son necesarias; extiende la vida útil de los activos industriales; mejora la eficiencia operativa y la productividad; reduce el inventario de piezas de repuesto; minimiza los riesgos de seguridad; y proporciona datos valiosos para la toma de decisiones estratégicas. Todo esto se traduce en un retorno de inversión significativo y en una ventaja competitiva para las empresas que implementan estas tecnologías avanzadas.
¿Qué tipos de sensores se utilizan en el mantenimiento industrial inteligente?
En el mantenimiento inteligente se emplean diversos tipos de sensores para analizar datos en tiempo real. Los más comunes incluyen sensores de vibración, que detectan anomalías en equipos rotativos; sensores térmicos, que identifican sobrecalentamientos; sensores ultrasónicos para detectar fugas; sensores de presión y caudal; sensores acústicos que captan sonidos anormales en maquinaria; sensores de corriente eléctrica para monitorizar el consumo energético; y acelerómetros que miden cambios en la velocidad. Estos dispositivos forman una red de monitorización continua que alimenta los sistemas de IA para predecir posibles fallos y minimizar el tiempo de inactividad en las instalaciones industriales.
¿Cómo implementar inteligencia artificial en la gestión de mantenimiento existente?
Para implementar inteligencia artificial en sistemas de gestión de mantenimiento existentes, recomendamos seguir estas etapas: primero, evalúa tu infraestructura actual e identifica áreas clave donde la IA puede generar mayor impacto; segundo, asegura que tienes capacidad para recopilar datos de calidad instalando sensores adecuados; tercero, selecciona soluciones de IA compatibles con tus sistemas actuales; cuarto, implementa proyectos piloto antes de un despliegue completo; quinto, capacita al equipo de mantenimiento para interpretar y actuar según las recomendaciones del sistema; y por último, establece métricas claras para medir el éxito. La implementación debe ser gradual y enfocada en resolver problemas específicos mientras se desarrollan las capacidades de análisis predictivo en tu organización.
¿Qué aplicaciones de la inteligencia artificial son más efectivas en el mantenimiento industrial?
Las aplicaciones de la inteligencia artificial más efectivas en el mantenimiento industrial incluyen la detección de anomalías, que identifica patrones inusuales en el funcionamiento de máquinas; el mantenimiento predictivo, que analiza datos históricos para pronosticar fallos antes de que ocurran; los gemelos digitales, que simulan equipos en entornos virtuales para optimizar su rendimiento; los sistemas de planificación de recursos que automatizan tareas de mantenimiento; los asistentes virtuales que proporcionan información técnica al personal; y el análisis de imágenes que detecta defectos mediante visión artificial. Estas soluciones mejoran la eficiencia operativa, reducen costos y minimizan el tiempo de inactividad al permitir intervenciones precisas y oportunas.
¿Cómo la IA en mantenimiento ayuda a optimizar los recursos industriales?
La IA en mantenimiento transforma la optimización de recursos industriales al analizar datos en tiempo real para tomar decisiones inteligentes. Mediante el aprendizaje automático, estos sistemas predicen con precisión cuándo ocurrirán fallos, permitiendo programar el mantenimiento justo cuando es necesario, ni antes ni después. Esto reduce las intervenciones innecesarias, optimiza el inventario de repuestos y extiende la vida útil de los equipos. Además, la IA prioriza las tareas de mantenimiento según su urgencia e impacto, asigna recursos humanos eficientemente y reduce el consumo energético al mantener los equipos en condiciones óptimas. El resultado es una significativa reducción de costos operativos y una mejora sustancial en la productividad general de las instalaciones.
¿Cuál es el futuro de la IA en el mantenimiento industrial?
El futuro de la IA en el mantenimiento industrial promete avances revolucionarios. Veremos sistemas cada vez más autónomos capaces de autocorregir problemas sin intervención humana y robots de mantenimiento que realizarán reparaciones en entornos peligrosos. La integración con tecnologías emergentes como blockchain garantizará la integridad de los datos de mantenimiento, mientras que la computación cuántica procesará grandes cantidades de datos con una velocidad sin precedentes. Los modelos de IA serán más explicativos, permitiendo entender mejor sus decisiones, y la realidad aumentada facilitará el trabajo del personal de mantenimiento. Todo esto llevará a una «fábrica cognitiva» donde la IA no solo predecirá fallos sino que también optimizará continuamente todos los procesos de mantenimiento, elevando la eficiencia industrial a niveles nunca antes vistos.
¿Qué desafíos presenta implementar sistemas de IA para el mantenimiento predictivo?
Implementar sistemas de IA para mantenimiento predictivo enfrenta varios desafíos importantes. Primero, la calidad y cantidad de datos: muchas industrias carecen de datos históricos suficientes o confiables para entrenar modelos precisos. Segundo, la integración con sistemas legados que no fueron diseñados para conectarse con tecnologías modernas. Tercero, la resistencia al cambio por parte del personal, que puede ver la IA como una amenaza a sus puestos. Cuarto, la inversión inicial significativa en sensores, infraestructura y software. Quinto, la necesidad de expertos que comprendan tanto el mantenimiento industrial como la ciencia de datos. Y sexto, los desafíos de ciberseguridad que surgen al conectar equipos industriales a redes. Superar estos obstáculos requiere una estrategia gradual, formación continua y un compromiso claro de la dirección con la transformación digital.
¿Cómo analizar datos de sensores para mejorar la eficiencia del mantenimiento industrial?
Para analizar datos de sensores eficazmente, comienza estableciendo líneas base de funcionamiento normal para cada equipo. Implementa sistemas que detecten anomalías en tiempo real comparando lecturas actuales con patrones históricos. Utiliza técnicas de aprendizaje automático para identificar correlaciones entre múltiples variables que podrían indicar problemas inminentes. Integra datos de diversas fuentes (vibración, temperatura, presión, etc.) para obtener una visión holística. Establece umbrales dinámicos que se ajusten según las condiciones operativas. Desarrolla dashboards visuales para que el equipo de mantenimiento interprete fácilmente los resultados. Lo más importante es evolucionar constantemente tus modelos analíticos, incorporando retroalimentación de los técnicos y resultados de intervenciones previas para mejorar continuamente la precisión predictiva y reducir el tiempo de inactividad.