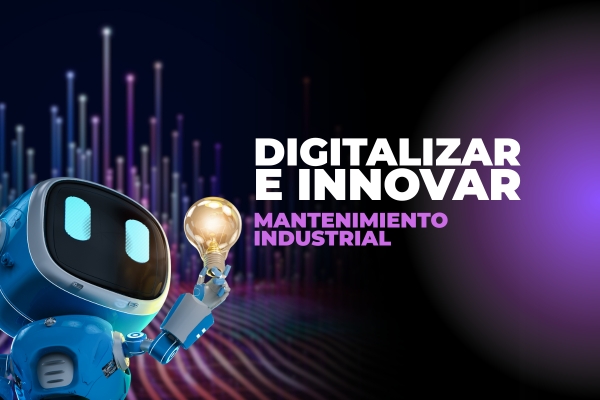
HercoTV
Podcast
Digitalizar e innovar en el área de mantenimiento se ha convertido en una necesidad estratégica para las empresas industriales que buscan competitividad. En esta guía te presentamos 6 pasos para digitalizar e innovar en el área de mantenimiento, con los que podrás optimizar procesos, reducir riesgos y aprovechar todo el potencial de la revolución tecnológica. Descubre cómo implementar soluciones avanzadas que transformen tu departamento de mantenimiento en un modelo de eficiencia y seguridad.
Sácale el máximo partido a la revolución tecnológica, reduce riesgos y haz tu departamento más eficiente
¿Te has encontrado alguna vez con la presión de conseguir que tu departamento funcione al máximo, mientras las averías se multiplican y los recursos se quedan cortos? ¿Sientes que inviertes demasiado tiempo en gestiones manuales o inspecciones peligrosas que podrían evitarse?
Si algo te suena familiar, la digitalización y la robótica avanzada pueden ser tus grandes aliadas. Innovar en mantenimiento no se trata solo de “estar a la moda”, sino de sobrevivir y destacar en un sector cada vez más competitivo, donde la seguridad y la eficiencia ya no son negociables.
Si no das el paso hacia la transformación digital, tu departamento corre el riesgo de quedarse atrás y perder, incluso, el activo más preciado: el talento humano. ¿Listo para conocer cómo puedes dar el salto sin perder el control ni arriesgar la operativa diaria?
Sigue leyendo, porque vamos a desglosar, paso a paso, cómo llevar la tecnología a tu área de mantenimiento de forma efectiva y segura.
¿Por qué digitalizar el área de mantenimiento? Beneficios directos y retos habituales
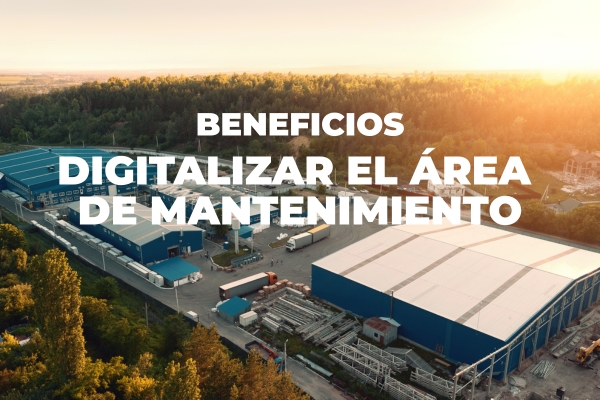
Empecemos por lo esencial: ¿para qué sirve realmente digitalizar e innovar en mantenimiento? La respuesta no está solo en los gadgets, sino en lo que puedes conseguir con ellos. Las tecnologías como robots inspectores, drones industriales o soluciones de inteligencia artificial no solo resuelven tareas repetitivas o peligrosas, sino que te permiten trabajar con datos fiables y predecir fallos antes de que sean un problema.
Hablamos de robots capaces de llegar a lugares de difícil acceso, drones que inspeccionan estructuras a decenas de metros sin poner en riesgo a nadie y software que anticipa cuándo un equipo va a fallar. Implementar estas soluciones aumenta la seguridad de los operarios, agiliza los tiempos de intervención y transforma radicalmente la recogida y análisis de datos.
No es una teoría: hay empresas que ya están reduciendo costes y, sobre todo, accidentes, gracias a la digitalización.
Eso sí, los retos iniciales existen. El principal suele ser el desconocimiento: no saber qué soluciones existen, o cómo encajar esas herramientas en los procesos ya establecidos. A esto se suma el miedo a la resistencia interna al cambio, especialmente si los equipos temen que la tecnología va a sustituirlos.
Pero hay certezas: bien implementada, la digitalización suma, nunca resta, y crea departamentos de mantenimiento más humanos y seguros.
Paso 1 | Evalúa tus necesidades de digitalización en mantenimiento
Antes de invertir en cualquier solución tecnológica, tienes que analizar detenidamente cómo funciona tu mantenimiento hoy. Pregúntate:
- ¿Qué tareas suponen un riesgo elevado para el personal?
- ¿Cuáles son manuales, repetitivas, y consumen tiempo?
- ¿En qué procesos recopiláis datos de forma poco eficiente o con margen de error?
A partir de ese diagnóstico, detecta las áreas donde implementar una nueva tecnología puede aportar un valor real. Por ejemplo, si tienes instalaciones de difícil acceso, plantéate si el uso de drones puede facilitar las inspecciones. Si tienes problemas recurrentes con controles manuales de equipos, ¿por qué no evaluar sensores inteligentes o soluciones IoT?
Consejo práctico: No asumas que la tecnología solo sirve para los grandes problemas. Muchas veces, los primeros avances se logran solucionando pequeños dolores del día a día que, acumulados, consumen recursos y generan frustraciones.
Paso 2 | Investiga soluciones tecnológicas para mantenimiento
Una vez identificadas las necesidades, llega el momento de comparar opciones. Tómate tu tiempo para analizar qué hay en el mercado: robots magnéticos para inspecciones verticales, drones con cámaras y sensores térmicos para supervisión en altura o espacios confinados, plataformas de gestión de mantenimiento asistidas por inteligencia artificial que convierten reportes en análisis predictivos y robots colaborativos (cobots) que trabajan codo con codo con el equipo humano en tareas específicas.
No todas las soluciones valen para todas las empresas; adáptate a tu tamaño, procesos y presupuesto. Consulta ferias industriales, publicaciones especializadas y comparte experiencias con colegas de otras empresas. Incluso, considera contactar con proveedores para obtener información sobre casos de éxito en sectores similares al tuyo.
Consejo práctico: No te dejes llevar solo por la novedad tecnológica. Busca aquellas herramientas que sean fáciles de usar, con interfaces intuitivas y que cuenten con soporte y formación cercana.
Paso 3 | Realiza una prueba piloto para validar herramientas
El siguiente paso, que muchas veces se pasa por alto, es testear la tecnología seleccionada en un entorno controlado. No es una cuestión de desconfianza, sino de minimizar riesgos y aprender de la experiencia de primera mano.
Propón un piloto de pequeña escala, con un grupo reducido que pruebe las nuevas herramientas en situaciones reales, pero sin comprometer la operativa general del departamento. Evalúa qué funciona, qué hay que adaptar y cómo responde el equipo. Durante este periodo, es clave recopilar datos: mide tiempos de intervención, seguridad, incidencias y la experiencia de los usuarios.
Este enfoque permite anticipar posibles problemas, ajustar procedimientos y, sobre todo, convencer a los más escépticos de los beneficios reales de la digitalización en su día a día.
Consejo práctico: Pide a los proveedores demostraciones y períodos de prueba. Así, el equipo gana confianza y puedes tomar una decisión fundamentada basada en experiencias reales.
Paso 4 | Forma a tu equipo en competencias digitales
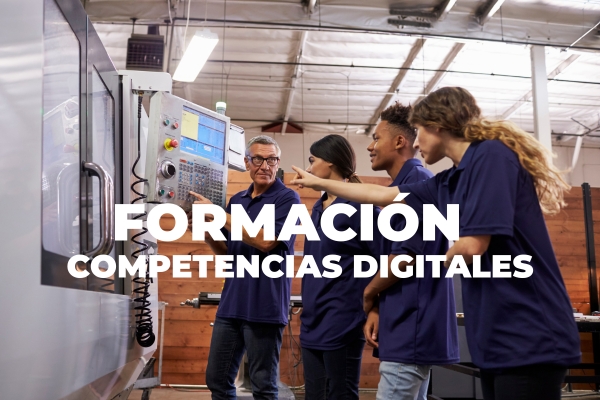
Una tecnología es tan buena como lo sean las personas que la usan. Por eso, invertir en formación es imprescindible para que tu equipo aproveche de verdad las herramientas digitales. El aprendizaje debe ser práctico y centrado en casos reales, favoreciendo el trabajo colaborativo entre el personal y los nuevos sistemas o dispositivos.
Organiza sesiones de formación personalizadas, desde guías de uso para los robots o drones, hasta workshops sobre análisis de datos y reporte digital. Lo importante no es solo formar a los técnicos, sino también a los supervisores y responsables, para que el cambio se gestione desde todos los niveles del área de mantenimiento. Recuerda que el mayor activo es tu gente; involúcralos y hazles partícipes del éxito de la implantación tecnológica.
Consejo práctico: Aprovecha el aprendizaje para disipar miedos sobre la “sustitución por máquinas”. Deja claro que la digitalización suma capacidades, libera tiempo para tareas de mayor valor y mejora notablemente la seguridad del equipo.
Paso 5 | Integra la tecnología de forma gradual y segura
Una vez superada la fase de prueba y con el equipo formado, pasa a una integración escalonada de la nueva tecnología en el proceso general. Este enfoque reduce resistencias, permite hacer ajustes y garantiza una adopción más natural y menos traumática.
Puedes empezar introduciendo la nueva herramienta en un solo turno o centro, y luego ampliarla por fases con los aprendizajes de cada etapa. Durante este periodo, es importante mantener canales de comunicación abiertos para recoger dudas, sugerencias y problemas que vayan surgiendo. Este “feedback” será oro para mejorar la implantación y lograr que la transformación digital se consolide.
Consejo práctico: Elabora un calendario de integración y acompáñalo de hitos medibles: número de intervenciones asistidas por tecnología, satisfacción del equipo, reducción de incidencias, mejora en tiempos de respuesta, etc.
Paso 6 | Analiza resultados para optimizar tu estrategia de digitalización
Para justificar la inversión y seguir mejorando, necesitas datos objetivos sobre el impacto de la tecnología en tu área de mantenimiento.
Elabora informes periódicos que evalúen la disminución de riesgos y accidentes como por ejemplo la eficiencia operativa de las tareas, el ahorro de costes en tiempo y recursos, la mejora en la calidad de la información recopilada y la satisfacción del personal junto con la facilidad de adopción de las nuevas herramientas.
No seas complaciente: usa los resultados para ajustar tu estrategia, buscar nuevas oportunidades de mejora y, si es necesario, invertir en actualizaciones o ampliar la gama de soluciones. Recuerda que la innovación digital es un proceso continuo que nunca se detiene.
Consejo práctico: Haz partícipe a todo el equipo de los logros. Cuando vean mejoras objetivas derivadas de la tecnología, aumentarán la implicación y el interés por nuevos proyectos de innovación.
Casos prácticos: ejemplos de éxito en la digitalización del mantenimiento
Las ventajas de digitalizar el mantenimiento ya no son promesas de futuro: son realidades palpables en numerosas empresas. Por ejemplo:
- Inspecciones sin riesgo: Antes, un técnico debía escalar decenas de metros para inspeccionar una torre de comunicaciones o una caldera industrial, con el consiguiente riesgo y tiempo empleado. Hoy, un dron realiza el trabajo en minutos, sin poner a nadie en peligro
- Optimización de recursos: Robots magnéticos trepan y examinan estructuras verticales, recopilando datos precisos y reduciendo el tiempo de parada de las instalaciones.
- Decisiones basadas en datos: Plataformas inteligentes convierten las alarmas y reportes en informes visuales fáciles de interpretar, permitiendo actuar antes de que se produzca el fallo y evitando gastos innecesarios.
Estos ejemplos ilustran cómo la tecnología transforma el trabajo en mantenimiento industrial, permitiendo equipos más seguros, ágiles y, lo más importante, humanos.
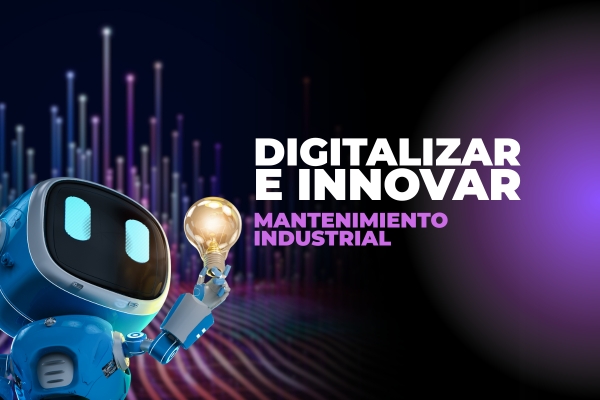
La importancia estratégica de digitalizar el mantenimiento hoy
Digitalizar el mantenimiento industrial ya no es una opción reservada a unos pocos visionarios; es una necesidad estratégica para cualquier responsable que quiera un departamento competitivo, eficiente y seguro. Vivimos un momento de auténtica revolución donde la tecnología no anula el factor humano, sino que lo multiplica.
Los expertos lo tienen claro: el mayor activo de un área de mantenimiento son las personas. Incorporar herramientas digitales y robóticas es protegerlas, darles tiempo y recursos para aportar más valor, y asegurar que el área de mantenimiento siga siendo la columna vertebral de la producción industrial.
Profundiza en la innovación: escucha el “Consejo del Experto”
¿Te gustaría escuchar de primera mano consejos prácticos sobre cómo llevar la innovación y la digitalización al área de mantenimiento industrial? No te quedes solo con la teoría: aquí te dejamos al final de este post la sección “El Consejo del Experto”, de la mano de Pedro Tapia, directamente extraído de nuestro podcast “Mantenimiento en Acción”.
Dedica unos minutos a ver el vídeo y descubre cómo los pasos que has leído se viven y aplican a pie de planta, con ejemplos claros y recomendaciones que puedes poner en práctica desde hoy.
Aprovecha este contenido exclusivo para inspirarte, resolver dudas y empezar a visualizar el cambio real que puede suponer para tu equipo y tus operaciones.
¡Suscríbete a nuestro canal de podcast “Mantenimiento en Acción” para no perderte ningún consejo, entrevista ni novedad del sector!
La transformación está a solo un click. ¿Te animas a dar el siguiente paso?
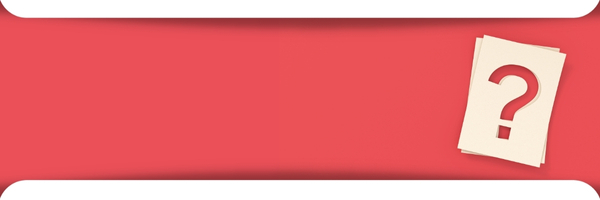
Preguntas frecuentes
¿Cómo digitalizar efectivamente el proceso de mantenimiento industrial?
No es solo instalar software; es repensar completamente cómo trabajas. Comienza evaluando tus puntos de dolor: ¿dónde pierdes más tiempo? ¿qué información necesitas pero nunca tienes a mano? El proceso debe abarcar desde la planificación hasta la ejecución y el análisis posterior. Lo fascinante es cómo digitalizar gradualmente: empieza por un área crítica, aprende de ella y expándete. Mi consejo: enfócate primero en digitalizar las operaciones que más impacto tengan en tu productividad. No busques perfección inicial, sino mejora continua que te permita optimizar recursos donde realmente importa.
¿Qué pasos debo seguir para implementar operaciones de mantenimiento digitalizadas?
Lo primero es conocer a fondo tus procesos de trabajo actuales, con sus fortalezas y debilidades. Después, debes crear una hoja de ruta clara, con objetivos medibles y plazos realistas. El éxito de los proyectos de digitalización depende de involucrar desde el principio a quienes usarán estas herramientas diariamente. Elige soluciones escalables que crezcan contigo y no te comprometas con tecnologías que te encierren en un solo proveedor. La eficacia del plan mejora drásticamente cuando avanzas por fases, celebrando victorias tempranas. Recuerda: la digitalización de procesos no es un destino, sino un viaje continuo de perfeccionamiento.
¿Cómo las tareas de mantenimiento pueden optimizarse mediante la digitalización?
La transformación digital elimina esos cuellos de botella que tanto nos desesperan. Las órdenes de trabajo dejan de perderse en montañas de papel para convertirse en asignaciones precisas, priorizadas automáticamente según urgencia e impacto. El trabajo de mantenimiento se vuelve predecible, permitiéndote optimizar la asignación de recursos y evitar tanto el exceso como la escasez de personal. La digitalización de los procesos te da visibilidad total: sabes exactamente qué se hizo, quién lo hizo y cuánto tiempo tomó. Esta transparencia te permite refinar continuamente tus estrategias de mantenimiento, identificando patrones que antes eran invisibles y transformando datos brutos en decisiones inteligentes.
¿Qué tecnologías son esenciales para lograr una digitalización efectiva en el mantenimiento de activos?
El corazón de tu transformación debe ser un robusto CMMS (sistema computerizado de gestión del mantenimiento) que centralice toda la información. Complementa esto con dispositivos y sensores inteligentes que monitorizan parámetros críticos en tiempo real, permitiendo detectar anomalías antes de que causen fallos. Las tecnologías digitales como gemelos digitales simulan escenarios «what-if» para optimizar decisiones. No subestimes el poder de la realidad aumentada para guiar reparaciones complejas o capacitar personal. Para una gestión de activos verdaderamente efectiva, necesitas estas herramientas trabajando en conjunto, creando un ecosistema donde la información fluye sin obstáculos entre sistemas, departamentos y niveles jerárquicos.
¿Qué es el mantenimiento predictivo y cómo puede transformar nuestras operaciones industriales por medio de la digitalización?
El mantenimiento predictivo puede revolucionar completamente tu operación al intervenir exactamente cuando se necesita, no antes ni después. Mientras el mantenimiento correctivo espera a que ocurra la falla y el preventivo se basa en calendarios fijos, el predictivo analiza patrones en tiempo real para determinar el momento óptimo de intervención. Imagina sensores que detectan una vibración anormal semanas antes de que cause una avería catastrófica, o algoritmos que predicen con precisión cuándo un componente alcanzará el final de su vida útil. Esto elimina el mantenimiento reactivo costoso y disruptivo, permitiéndote planificar intervenciones durante paradas programadas, maximizando la disponibilidad de tus activos.
¿Qué beneficios ofrece un software de mantenimiento para la gestión de mantenimiento?
Un buen GMAO transforma radicalmente tu día a día operativo. Primero, centraliza toda la información, eliminando esos frustantes «no encuentro el historial» que todos hemos sufrido. Las órdenes de trabajo se generan, asignan y rastrean automáticamente, reduciendo errores y duplicidades. Tu personal de mantenimiento gana autonomía con toda la información necesaria en sus dispositivos móviles. La gestión del mantenimiento se vuelve proactiva en vez de reactiva, permitiéndote reducir el tiempo de inactividad hasta en un 30%. Los informes que antes te tomaban días se generan en segundos, dándote una visibilidad sin precedentes sobre KPIs cruciales. Esto no solo mejora la eficiencia, sino que transforma radicalmente tu toma de decisiones.
¿Cómo el mantenimiento inteligente está cambiando el futuro del mantenimiento?
La revolución de la Industria 4.0 está redefiniendo lo que significa «mantenimiento». Estamos pasando de intervenir cuando algo falla a predecir fallos con semanas de anticipación. Los sistemas actuales no solo registran qué sucedió, sino que aprenden continuamente de los registros de mantenimiento históricos para mejorar sus predicciones. El mantenimiento preventivo tradicional está evolucionando hacia uno basado en condiciones reales, eliminando intervenciones innecesarias. Los tiempos de inactividad se reducen drásticamente mientras la precisión aumenta. La inteligencia artificial analiza patrones imperceptibles para el ojo humano, detectando anomalías sutiles que anuncian problemas futuros. No es ciencia ficción: es la realidad actual de las plantas más competitivas.
¿Cuáles son las principales barreras al implementar operaciones de mantenimiento digitalizadas?
La resistencia al cambio suele ser el primer obstáculo que enfrentarás. Tus equipos o personas pueden ver estas nuevas herramientas como una amenaza a sus años de experiencia. La seguridad de los datos emerge como otra preocupación crítica: ¿dónde se almacena la información sensible de tu planta? También subestimamos frecuentemente la importancia de una buena experiencia de usuario; si el sistema es complicado, será abandonado rápidamente. El uso de herramientas digitales requiere nuevas competencias que tu equipo puede no tener inicialmente. Por último, muchas empresas caen en la trampa de digitalizar procesos deficientes, perpetuando problemas en vez de resolverlos. La tecnología amplifica tanto lo bueno como lo malo.
¿Cuál es el futuro del mantenimiento y cómo prepararse para él?
El horizonte del mantenimiento de planta apunta claramente hacia sistemas autónomos capaces de auto diagnosticarse y, en algunos casos, auto repararse. Las soluciones digitales evolucionarán hacia ecosistemas completamente integrados donde el mantenimiento asistido por ordenador colaborará con producción para eliminar las paradas no planificadas. Los gemelos digitales simularán escenarios complejos, optimizando decisiones antes de implementarlas físicamente. Para prepararte, empieza hoy fortaleciendo el flujo de información entre departamentos, desarrollando competencias digitales en tu equipo y, sobre todo, cultivando una mentalidad de mejora continua. El futuro pertenece a quienes ven en los datos no solo números, sino oportunidades para transformar completamente la productividad industrial.