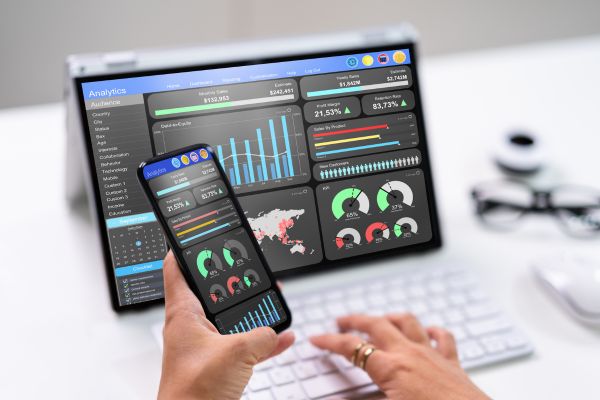
HercoTV
Podcast
Cómo optimizar el mantenimiento industrial: Medición y análisis de datos
¿Alguna vez has sentido que el mantenimiento de tu planta industrial es un gasto constante y poco controlado? Muchas empresas operan sin un control detallado de sus averías y costos de mantenimiento, lo que les impide optimizar recursos y reducir gastos innecesarios. Pero déjanos decirte que esto puede cambiar de inmediato, sin coste adicional, siempre que lo realices correctamente.
La clave está en medir y analizar los datos de mantenimiento. Implementar sistemas de medición y análisis permite identificar patrones, priorizar acciones y transformar el mantenimiento de un gasto a una inversión estratégica. En este artículo, profundizamos sobre la conversación que mantuvimos con David Sánchez de QualityMan Group en nuestro podcast «Cómo optimizar la gestión del mantenimiento en tu empresa». Vamos a profundizar sobre las técnicas para optimizar los costos, mejorar la toma de decisiones y aumentar la eficiencia operativa de tu planta.
Datos: La materia prima del mantenimiento eficiente
Imagina que eres un chef y quieres preparar el mejor plato posible. ¿Cómo lo harías? Primero, recopilarías información sobre los ingredientes: sus cantidades, calidad, frescura, etc. Luego, analizarías esos datos para determinar la mejor receta y técnicas de cocción. Del mismo modo, para optimizar el mantenimiento de tu planta, necesitas recopilar y analizar datos clave.
Algunos de los datos más importantes a medir son:
- Tiempos de parada y averías.
- Costos de mantenimiento preventivo, correctivo, piezas de repuesto, etc.
- Indicadores de fiabilidad y disponibilidad de los equipos.
- Eficiencia energética y consumos.
- Resultados de inspecciones y diagnósticos.
Recopilar estos datos de forma sistemática te permitirá identificar problemas recurrentes, cuellos de botella y oportunidades de mejora. Pero no te quedes ahí, el verdadero poder está en el análisis.
Análisis: Transformando datos en acciones estratégicas
Una vez que tengas tus datos, es hora de sacarles el máximo provecho. Empieza por identificar patrones y tendencias. ¿Hay equipos que fallan con más frecuencia? ¿En qué momentos se concentran la mayoría de las paradas? ¿Cuáles son los costos más elevados y por qué?
Utiliza herramientas de análisis avanzadas, como el análisis de regresión o los modelos de fiabilidad, para entender las causas raíz de los problemas. Esto te permitirá tomar decisiones informadas sobre dónde enfocar tus esfuerzos de mantenimiento.
Por ejemplo, si detectas que un determinado equipo tiene un alto índice de fallos, podrías analizar si es necesario aumentar la frecuencia de mantenimiento preventivo o si es más rentable reemplazarlo por uno más fiable. O si identificas picos de consumo energético, podrías optimizar los programas de mantenimiento de los sistemas de climatización y reducir así tus costos operativos.
Del análisis a la acción: Optimiza la gestión y el costo de mantenimiento
Una vez que hayas identificado las áreas de mejora, es hora de pasar a la acción. Utiliza los datos y análisis para desarrollar un plan de mantenimiento optimizado que te permita:
- Reducir costos: Prioriza las actividades de mantenimiento en función de su impacto en la fiabilidad y el costo. Elimina tareas innecesarias y enfócate en lo que realmente importa.
- Mejorar la disponibilidad: Ajusta los programas de mantenimiento preventivo para minimizar las paradas imprevistas. Anticípate a los fallos y planifica las intervenciones de manera eficiente.
- Aumentar la eficiencia: Optimiza el uso de recursos, como mano de obra y repuestos, en base a los datos históricos. Evita tener inventarios excesivos y asegura la disponibilidad de lo necesario.
- Tomar mejores decisiones: Utiliza los análisis para fundamentar tus decisiones de mantenimiento, desde inversiones en nuevos equipos hasta la contratación de personal especializado.
Recuerda, el mantenimiento no es un gasto, sino una inversión estratégica. Al medir, analizar y optimizar tus procesos, no solo reducirás costos, sino que también mejorarás la fiabilidad, la eficiencia y la competitividad de tu planta.
Gestión de las relaciones y cultura de mejora continua en la gestión del mantenimiento
Implementar un sistema de medición y análisis de datos de mantenimiento no es solo una cuestión técnica, también implica un cambio cultural en tu organización. Como líder, debes fomentar una mentalidad de mejora continua y toma de decisiones basada en datos.
Involucra a todo tu equipo de mantenimiento en este proceso. Capacítalos en el uso de herramientas de análisis y motívalos a participar activamente en la identificación de oportunidades de mejora. Crea un entorno donde los errores se vean como oportunidades de aprendizaje, no de culpa.
Además, asegúrate de que los datos y análisis fluyan de manera transparente a través de toda la organización. Comparte tus hallazgos y planes de acción con la dirección, producción, calidad y otras áreas clave. Esto no solo generará confianza, sino que también permitirá una toma de decisiones más coordinada y efectiva.
El futuro del mantenimiento está en los datos
En un mundo cada vez más competitivo, el mantenimiento ya no puede ser visto como un simple gasto, sino como una inversión estratégica que impacta directamente en la rentabilidad y la sostenibilidad de tu negocio. Y la clave para optimizar esa inversión está en la medición y el análisis de datos.
Al implementar un sistema de medición y análisis de mantenimiento, no solo reducirás costos, sino que también mejorarás la fiabilidad de tus equipos, la eficiencia de tus procesos y la toma de decisiones en toda la organización. Serás capaz de anticipar problemas, priorizar acciones y transformar el mantenimiento en una ventaja competitiva.
Así que, ¿estás listo para liderar este cambio en tu empresa? El futuro del mantenimiento industrial está en tus manos. Empieza a medir, analizar y optimizar hoy mismo, y prepárate para llevar tu planta al siguiente nivel de excelencia operativa.
Preguntas para tu reflexión
- ¿Qué datos de mantenimiento recopilas actualmente en tu empresa? ¿Cómo podrías mejorar la calidad y el alcance de esa información?
- ¿Qué herramientas de análisis de datos utilizas para identificar oportunidades de mejora en tu programa de mantenimiento? ¿Cómo podrías aprovechar mejor esos análisis?
- ¿Cómo podrías involucrar a todo tu equipo de mantenimiento en la cultura de mejora continua basada en datos? ¿Qué acciones específicas podrías implementar?
Si buscas apoyo para aplicar estas estrategias, te recomendamos escuchar la entrevista a David Sánchez que mencionamos al inicio de este artículo. También puedes acceder a todos los episodios de «Mantenimiento Acción» en Spotify. Estamos aquí para ayudarte a construir un equipo de mantenimiento más comprometido, eficiente y productivo.
Here’s an extended FAQ in Spanish for the topic «Medir y analizar: La clave para optimizar el mantenimiento» using the specified format and incorporating the provided terms:
¿Cuáles son los principales indicadores de mantenimiento que debemos medir?
Los principales indicadores de mantenimiento incluyen MTBF (Tiempo Medio Entre Fallos), MTTR (Tiempo Medio de Reparación), disponibilidad de equipos, costo de mantenimiento por unidad de producción, y cumplimiento del plan de mantenimiento preventivo. Estos KPI de mantenimiento son fundamentales para evaluar la eficacia de nuestra estrategia de mantenimiento y la confiabilidad de los activos.
¿Cómo puede el mantenimiento predictivo mejorar la gestión de activos?
El mantenimiento predictivo mejora significativamente la gestión de activos al anticipar fallos antes de que ocurran. Utilizando tecnologías avanzadas y análisis de datos, podemos predecir cuándo un equipo necesitará mantenimiento, lo que reduce el tiempo de inactividad, optimiza el ciclo de vida de los activos y disminuye los costos de mantenimiento a largo plazo.
¿Qué papel juega el software en la optimización del mantenimiento?
El software de gestión de mantenimiento es crucial para optimizar las operaciones. Permite un control eficiente de las órdenes de trabajo, facilita la planificación del mantenimiento, ayuda en el análisis de datos para el mantenimiento predictivo, y proporciona informes detallados sobre el rendimiento del mantenimiento, todo lo cual contribuye a una gestión de mantenimiento más eficaz y a la toma de decisiones informadas.
¿Cómo se puede implementar una estrategia de mantenimiento centrado en la fiabilidad?
Para implementar un mantenimiento centrado en la fiabilidad, debemos: 1) Identificar los activos críticos, 2) Analizar los modos de fallo potenciales, 3) Priorizar las acciones de mantenimiento basadas en el riesgo, 4) Desarrollar planes de mantenimiento preventivo y predictivo, 5) Capacitar al personal en nuevas técnicas, y 6) Utilizar software para monitorear y analizar continuamente el rendimiento de los equipos.
¿Cuál es la diferencia entre mantenimiento preventivo y mantenimiento correctivo?
El mantenimiento preventivo se realiza de forma programada para prevenir fallos antes de que ocurran, mientras que el mantenimiento correctivo se lleva a cabo después de que se ha producido un fallo. Ayuda a reducir el tiempo de inactividad no planificado y a extender la vida útil de los equipos, mientras que el mantenimiento correctivo es reactivo y generalmente más costoso a largo plazo.
¿Cómo podemos utilizar los datos de mantenimiento para mejorar la confiabilidad de los activos?
Los datos son invaluables para mejorar la confiabilidad de los activos. Podemos analizarlos para identificar patrones de fallo, optimizar los intervalos de mantenimiento, predecir fallos futuros, y tomar decisiones informadas sobre la sustitución o mejora de equipos. Un análisis detallado de estos datos nos permite ajustar continuamente nuestra estrategia de mantenimiento para maximizar la confiabilidad y el rendimiento de los activos.
¿Qué beneficios ofrece el mantenimiento basado en la condición?
El mantenimiento basado en la condición ofrece numerosos beneficios, incluyendo: reducción de paradas no planificadas, optimización de los costos de mantenimiento, aumento de la vida útil de los equipos, mejora de la seguridad operativa, y una planificación más eficiente de las intervenciones de mantenimiento. Este enfoque nos permite realizar mantenimiento solo cuando es necesario, basándonos en el estado real del equipo, lo que resulta en una gestión de mantenimiento más eficiente y efectiva.
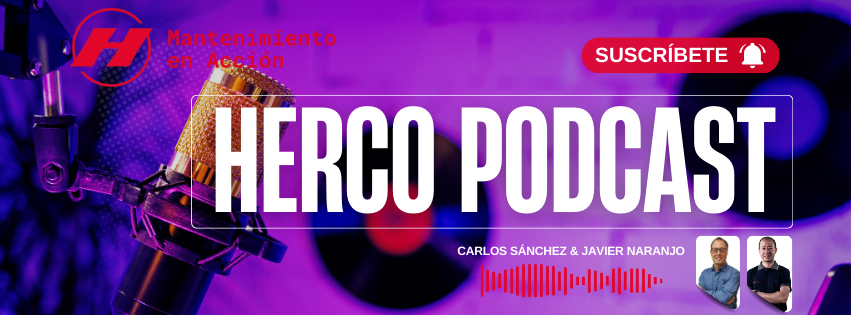